[ad_1]
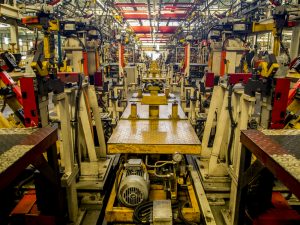
An assembly line at a car factory in Samutprakarn, Thailand.
Credit: Depositphotos
Ten years ago, Thailand could easily claim the title of being the undisputed automobile manufacturing hub in Southeast Asia. COVID-19 has changed everything in the short term, but even before the pandemic Indonesia was starting to pose a credible challenge to Thailand’s industry dominance. Once the dust settles, will Thailand retain its position atop the regional automobile manufacturing industry? To answer that question, we first need to consider how it got there to begin with.
The mass production of automobiles has been a major goal for emerging markets in Southeast Asia for decades. Building a car involves complex and integrated supply chains that provide hundreds of thousands of jobs, draw in billions of dollars of investment, and require the kinds of skill and technology transfers that contribute to long-term growth. Moreover, early industrializers like South Korea and Japan became global economic leaders, in part, by mastering the production and export of automobiles. It’s a model that many other countries seek to emulate.
But how does a country become a car manufacturing hub? Malaysia tried to do it with a national car company. The government erected trade barriers that made it prohibitively expensive to import foreign cars and then sought to develop a locally designed and manufactured automobile, the Proton. The Proton has a commanding share of the captive Malaysian market, but very little presence outside of it. Because the market is already saturated with Protons, there is a ceiling on how much growth can be drummed up domestically. By focusing on boosting domestic industry behind protectionist barriers, Malaysia did build its national car, but it’s not terribly competitive when it has to go toe-to-toe with global rivals.
Thailand went the other route, following the IMF and WTO playbook during the 1990s and opening up its supply chains to foreign investment and imports. In 1995, Thailand produced around 600,000 cars, almost all of which were sold to local Thai consumers. By 2015, Thailand was producing 1.9 million cars, with 800,000 domestic sales and 1.2 million exports. Because Thailand offered attractive investment incentives and allowed foreign automakers more freedom in how they organized their supply chains, Thai factories were able to specialize and improve their efficiency, making their car exports the most competitive in the region.
Indonesia followed a path that was somewhere between the two. In the 1970s and 1980s it erected stiff protectionist barriers and mandated local content requirements in an unsuccessful attempt to grow the domestic auto manufacturing industry. The government began experimenting with liberal market reforms in the 1990s, but then did an about-face when President Suharto’s son Tommy was placed in charge of Indonesia’s own newly created national car company, Timor Putra Nasional. With the onset of the Asian Financial Crisis in 1997, the company collapsed and Indonesia pivoted back to market reforms.
But it wasn’t until around the mid-2000s, when post-crisis per capita GDP started to bounce back in earnest, that Indonesia’s auto industry finally began to get its legs. The car business is very sensitive to economies of scale: the more orders you have, the more efficient it is to do big production runs. This is why it is so hard to jump-start the industry behind protectionist barriers, because you need a minimum level of demand before the business can become economically viable. Thailand, by specializing and liberalizing, was able to ride global demand because its exports were cheap.
Indonesia’s auto sector, by comparison, really took off on the strength of its domestic demand, which exploded from 486,000 in 2009 to 1.2 million in 2014. Because factories in Indonesia were scaling up production so quickly to meet ballooning local demand, they were able to capitalize on more efficient economies of scale and Indonesian exports finally became competitive. Indonesia has been a net exporter of cars since 2013, exporting 332,000 in 2019. Unlike Thailand, production didn’t ramp up to meet export demand. Instead, exports were a knock-on effect of roaring domestic sales.
Total production in Indonesia reached a high of 1.3 million in 2018, lagging Thailand by several hundred thousand units, so for now Thai auto manufacturers retain the edge. But this regional competition to lead the industry does underline some interesting questions about whether export-led growth that hinges on external demand is a preferable development model to growth powered by internal demand. If Indonesia’s economy continues to grow the way people expect it to over the coming years – and as long as a sufficient share of the national income ends up in the hands of people who will spend it on consumer goods – we may have a clearer answer to that question soon.
[ad_2]
Source link